- 26 Aprile 2012
- 10,671
- 9,269
Negli ultimi mesi ho ricevuto un po' di materiale sull'aereo che, nel bene o nel male, sta modificando l'aviazione civile mondiale: il 787. Si tratta di materiale sparso, proveniente da varie fonti: reportages da parte di colleghi che sono stati a Seattle da Boeing, notizie interne da parte del nostro delivery manager che segue Boeing, articoli apparsi sulla stampa generalistica. Li ho letti, salvati in una cartella e dimenticati, finchè non ho incontrato un tizio, in aeroporto, cn cui ho iniziato a parlare di aerei e aviazione. Un personaggio con un grande bagaglio di conoscenza (forse anche a causa della tessera Senator Lufthansa), finchè, parlando del 787 e dei suoi ritardi, non ha detto qualcosa di particolare: "non capisco perchè ci abbia messo cosí tanto tempo ad arrivare. Alla fine, è un aereo convenzionale". Grazie alle mie letture sapevo che non era cosí, e avrei voluto spiegarglielo, ma sono dovuto andare.
Di conseguenza, ho riscoperto i miei articoli sul 787 e ho cercato di metterli insieme, dandogli un senso organico, con uno scopo: dimostrare, con un po' di dati e di dettagli (ricordo che non sono per niente un esperto, semmai un buon ascoltatore), quanto il 787 sia differente dagli altri aerei attualmente in circolazione e razza di "salto" sia il passaggio da aerei moderni, come 777 e 330 al Dreamliner.
Di seguito troverete le fasi in cui il post è diviso:
- Soluzioni tecniche
- Produzione
- Uso e handling quotidiano
Tutte con una particolare attenzione alle differenze esistenti con gli aerei di oggi.
Soluzioni tecniche
Il 787 è un aereo fondamentalmente differente da tutti i suoi predecessori, almeno in campo civile. Prima di lui, infatti, la stragrande maggioranza delle superfici di un aereo era in alluminio, con materiali compositi qua e là in aree periferiche (in senso spaziale, beninteso, non d'importanza). Per fare un esempio, il 777 ha un quantitativo di materiali compositi pari a meno del 12% del proprio peso, con composti di grafite usati nelle superfici di comando della coda, ali, coperture dei motori e nei portelli che ricoprono i vani carrelli. Più del 50% del peso del 777 è composto di leghe di alluminio.
Spaccato del Boeing 777-200
Il 787, invece, ribalta letteralmente queste cifre.il 50% delle sue superfici sono in materiali compositi, per lo più fibre di carbonio disposte in strati successivi, e solo il 20% è in alluminio. Un considerevole 15% è titanio, concentrato soprattutto nei critici piloni subalari che reggono i motori.
L'inversione di queste proporzioni è un cambio pressochè totale, che ha comportato grandi differenze nelle metodologie produttive nonchè grandi difficoltà. Prima del 787, per esempio, non si sapeva bene come legare materiali cosí esotici insieme, facendoli rimanere insieme anche se sottoposti alle fortissime sollecitazini subite da un aereo in volo: Ricorderete di sicuro, credo, i ritardi generati dai problemi trovati nel raccordo "a cassa" che unisce l'ala alla fusoliera, che continuava a separarsi in strati come una torta millefoglie.
Ed ecco il raccordo "colpevole"
Optare per i materiali compositi ha un effetto sicuramente positivo sui pesi, dato che il carbonio è più leggero, flessibile e resistente delle leghe di alluminio usate solitamente per la fusoliera degli aerei. Ci sono, però, delle controindicazioni, e nemmeno di poco conto. Una di queste è la difficoltà che si incontra nel "legare" insieme materiali così diversi, un problema che ha afflitto Boeing a lungo, al punto che il primo 787 ad uscire dalla catena di montaggio, salutato dal Presidente Obama, aveva dei giunti ("fasteners", non saprei come chiamarli in italiano) inadatti agli usi aeronautici e, pare, acquistati dagli ingegneri Boeing in un negozio della catena Home Depot. Un po' come se la Fiat presentasse la nuova 500 con dei bulloni comprati a Leroy Merlin, per capirci.
Altri problemi riguardano la costruzione dell'aereo in sé, che viene sostanzialmente "tessuto" da un enorme telaio intorno a una cassaforma, poi "cotto" e infine modificato col taglio al laser dei finestrini e di tutte le aperture come portelli e così via. Ogni pezzo viene ispezionato visivamente per assicurarsi che l'amalgama di fibre, resine e colle sia perfetto.
Un aneddoto che mi è stato raccontato e che mi limito a riportare qui, senza poterne confermare la veridicità o meno, dice che la FAA americana abbia costretto Boeing a inserire degli "O ring" metallici, un po' come l'ossatura degli aerei convenzionali, per irrobustire la struttura dell'aereo, rivettandoli alla fusoliera in compositi. Questi anelli non sarebbero stati necessari, secondo Boeing, ma essendo la tecnologia così nuova e rivoluzionaria le autorità hanno preferito non correre rischi.
parlando di non correre rischi... Questo è il risultato delle modificazioni per le batterie agli ioni di litio
Un altro problema sono i fulmini. Come forse saprete, gli aerei sono colpiti dai fulmini almeno una volta all'anno, dato che sono l'unica cosa metallica in giro per i cieli. Non è un porlema, i lightning checks sono qualcosa che gli ingegneri sono abituati a compiere e anche l'effetto sui sistemi di bordo è irrisorio, dato che tutto è a doppia o tripla ridondanza. Inoltre gli aerei sono accuratamente schermati, essendo vere e proprie gabbie di Faraday, il che fa sì che la carica elettrica del fulmine possa correre da prua a poppa senza problemi, finendo scaricata dalle prese statiche (quelle piccole antennine che si vedono sulle ali). L'unica parte dell'aereo che non è in metallo è il radome, che non è altro che una specie di guscio di materiale simile alla cellulosa sagomato a nido d'ape; ciononostante, persino quella parte dell'aereo è schermata, grazie a delle lamelle metalliche che corrono verso il muso del radome.
Tutti questi accorgimenti, sul 787, non sono possibili. Il 787 è fatto di grafite e altri materiali non metallici, che non consentono una buona conduzione dell'elettricità. Un possibile fulmine su un aereo del genere avrebbe effetti disastrosi sull'aereo e sui passeggeri a bordo. La soluzione trovata dagli ingegneri Boeing è altamente sofisticata, e prevede di inserire filamenti di rame nel "tessuto" dei compositi, rendendo così l'aereo un buon conduttore pur non essendo metallico.
Un'altra grande differenza che distingue il 787 dal resto del mondo è l'elettricità. Tutti gli aerei generano elettricità, con l'APU e i motori (le turbine fanno girare dei generatori che forniscono l'elettricità di bordo, usata in gran parte per alimentare i sistemi IFE). Il 787 genera piu’ di tre volte l’elettricita’ prodotta dal 777 e la maggioranza e’ in corrente continua (piu’ pericolosa dell’alternata, ovviamente). La necessita’ di dover generare piu’ energia elettrica sta, in parte, nella natura fortemente elettronica dell’aereo, il cui cockpit e’ interamente coperto da pannelli LCD multifunzione e che “dialoga” via WiFi con i servizi di terra, ma anche perche’ il 787 e’ un aereo bleedless; in sostanza, non funziona con questo schema:
secondo cui i motori di un aereo hanno un particolare compressore che spinge l’aria dalle turbine a un circuito col quale si alimentano generatori, sistemi pneumatici per il controllo di varie parti dell’aereo, il deicing e soprattutto l’aria condizionata di bordo.
Il 787, invece, usa generatori posizionati nei motori (4) e due APU. I generatori collocati nei motori alimentano dei bus in corrente continua che, a loro volta, supportano tutti quei sistemi che prima, erano supportati dai sistemi pneumatici Bleed Air. Per dire, anche i freni sono elettronici!
Il vantaggio di non avere un systema Bleed Air e’ riconducibile alla maggior efficienza in termini di consumi, riduzione dei costi di manutenzione (i sistemi bleed sono notoriamente stronzi da riparare, o almeno cosi’ mi e’ stato detto, dato che bisogna praticamente smontare un motore per accedervi), riduzione dei pesi e, in generale, una maggior facilita’ di utilizzo una volta fatto il “cambio” di mentalita’. Gli svantaggi? Beh, i sistemi elettrici sono meno affidabili di quelli meccanici; bisogna stare attenti alla sicurezza, perche’ stiamo parlando di potenze fino a 540v in corrente continua, roba che uccide, e in generale il costo e’ maggiore. Sappiamo tutti quanto costa farsi riparare un cambio meccanico o uno elettroattuato.
Produzione
In principio il pioniere era Airbus. Il consorzio europeo, infatti, ha creato una delle più complesse (e efficaci) supply chain del mondo, applicando i principi lean all'aviazione civile come mai nessuno prima di quel momento.
Boeing ha sempre prodotto buona parte dei suoi aerei negli USA, se escludiamo componentistica minore e il supporto delle cosiddette "Japanese Heavies" (Mitsubishi su tutte). Il 787 è differente, dato che ha una supply chain che copre almeno tre continenti. Il motivo dietro a questo cambio di politica è duplice: innanzitutto beneficiare dell'esperienza maturata da alcuni costruttori in certi campi e, soprattutto, arraffare quanti più sussidi possibili senza trovarsi l'Unione Europea a protestare al WTO: non è un segreto, infatti, che le Heavies giapponesi sono pesantemente supportate dal governo di Tokyo.
Trucchetti fiscali a parte, la supply chain del 787 è enorme, come mostra questa foto, e la cosa più stupefacente è che funziona. Chiaro, ora la situazione non è delle migliori a causa dei ritardi dovuti alle batterie, ma in generale la catena di montaggio ha dimostrato di saper funzionare, con pezzi in arrivo da posti lontani come l'Italia o il Giappone che appaiono sula linea al giusto momento, nella giusta posizione e nella giusta quantità.
La costruzione dell'aereo in sè è un altro miracolo della produzione lean: ho trovato questo schema, che un collega ha messo insieme dopo essere andato a visitare Seattle, in cui un 787 viene costruito in circa 40 giorni di cycle time. Se pensiamo a cosa sta dietro, alla monumentalità dell'operazione e al fatto che tutto questo non succede per un solo aereo, ma peralmeno una cinquantina di aerei all'anno c'è solamente da rimanere sbalorditi. L'uomo, e so di scrivere qualcosa di veramente nerd, sa macchiarsi delle peggio porcate ma, allo stesso tempo, riesce anche a produrre meraviglie del genere. Anche questa è una "prima" mica da ridere per l'aviazione civile mondiale.
Uso e handling quotidiano
Gli aerei di oggi sono stati costruiti, ideati, negli anni '90, quando i telefonini si portavano nelle valigette, l'unico tablet era stato intravisto in qualche fotogramma di "2001: Odissea nello Spazio" e non esisteva il WiFi. Il 787 è, invece, figlio di quest'epoca, e poco ci manca che non abbia il suo account Twitter per postare i suoi status a amici e followers.
Il risultato è una vera e propria rivoluzione copernicana per chiunque abbia a che fare con l'aereo a terra. Iniziamo con persone come loaders, catering e pulizie, senza dimenticarci dei turnround managers: tutta gente che deve attaccare qualcosa all'aereo: camion, high lifts, elevators, belt conveyors, jetways... Tutta roba di metallo, parecchio pesante, che viene accostata a un aereo. Si tratta di manovre molto delicate, dato che basta perdere un attimo il pedale della frizione per sbattere contro l’aereo e fare danni anche importanti.
Il problema per il 787 e la sua fusoliera in compositi e’ che i danni non sono immediatamente visibili. A differenza di un normale aereo, come questo 747 colpito da delle scalette lasciate non completamente frenate durante una giornata di vento, il buco sulla fusoliera non e’ visibile ad occhio nudo e, peggio ancora, non e’ riparabile con una semplice “pezza” rivettata sulla fusoliera.
Bisogna, infatti, portare l’aereo in hangar, controllare la trama e l’ordito del “tessuto” con degli strumenti appositi come quelli qui sotto, e agire di conseguenza. Se il danno e’ piccolo si possono introdurre delle schiume specifiche, se il danno e’ grave... meglio non pensarci.
Altri problemi riguardano il layout dell’aereo in se’. Il 787-8 e’ un aereo con 4 uscite, e di solito le jetways attraccano alla porta 2L che, su questo modello, e’ pero’ molto vicina al margine dell’ala, rendendo l’attracco difficile. Anche la 1L non e’ cosi’ facile da avvicinare, dato che la flangia della jetway si troverebbe a meno di quaranta centimetri da una particolare antenna, quella dell’orizzonte artificiale.
Il grosso vantaggio per un ingegnere, pero’, e’ quello di sapere subito come un aereo “sta” al momento dell’arrivo. Il 787 puo’, come dicevo, dialogare via WiFi con i computer degli ingegneri in ufficio sin dall’atterraggio, prima ancora di arrivare on stand. Cosi’ gli ingegneri sanno subito cosa c’e’ che non va e possono intervenire immediatamente, portandosi i pezzi di ricambio direttamente sullo stand.
Conclusione
Seven-Late-Seven, l’aereo che riesce a prendere fuoco da solo, la croce della Boeing... Gli appellativi per il 787 si sono sprecati. L’opinione generale sembra quella del personaggio che ho incontrato quel giorno in aeroporto, qualche mese fa: “Com’e’ possibile che, per costruire un aereo che non sembra poi cosi’ diverso dagli altri, ci abbiano messo cosi’ tanto?”
La realta’ e’ che questo aereo e’ diverso in tutto, sottopelle e anche al di sopra. Quando cambiamenti di questa portata vengono apportati, tutti insieme e in un progetto che si spande su quattro continenti, e’ ovvio che ci saranno ritardi, cambiamenti e problemi.
Spero che queste due pagine vi abbiano aiutato a cambiare idea sul Dreamliner, un po’ come hanno aiutato me. E, per finire, una piccola chicca: una preview, limitata devo purtroppo, della Club sui 787 e A380.
Fonti
- The Boeing Corporation
- British Airways
- Robert Dorrell
- Airliners.net - Russian Spotter Team
Di conseguenza, ho riscoperto i miei articoli sul 787 e ho cercato di metterli insieme, dandogli un senso organico, con uno scopo: dimostrare, con un po' di dati e di dettagli (ricordo che non sono per niente un esperto, semmai un buon ascoltatore), quanto il 787 sia differente dagli altri aerei attualmente in circolazione e razza di "salto" sia il passaggio da aerei moderni, come 777 e 330 al Dreamliner.
Di seguito troverete le fasi in cui il post è diviso:
- Soluzioni tecniche
- Produzione
- Uso e handling quotidiano
Tutte con una particolare attenzione alle differenze esistenti con gli aerei di oggi.
Soluzioni tecniche
Il 787 è un aereo fondamentalmente differente da tutti i suoi predecessori, almeno in campo civile. Prima di lui, infatti, la stragrande maggioranza delle superfici di un aereo era in alluminio, con materiali compositi qua e là in aree periferiche (in senso spaziale, beninteso, non d'importanza). Per fare un esempio, il 777 ha un quantitativo di materiali compositi pari a meno del 12% del proprio peso, con composti di grafite usati nelle superfici di comando della coda, ali, coperture dei motori e nei portelli che ricoprono i vani carrelli. Più del 50% del peso del 777 è composto di leghe di alluminio.
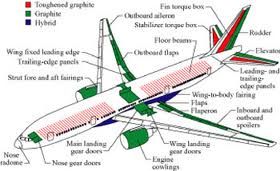
Spaccato del Boeing 777-200
Il 787, invece, ribalta letteralmente queste cifre.il 50% delle sue superfici sono in materiali compositi, per lo più fibre di carbonio disposte in strati successivi, e solo il 20% è in alluminio. Un considerevole 15% è titanio, concentrato soprattutto nei critici piloni subalari che reggono i motori.
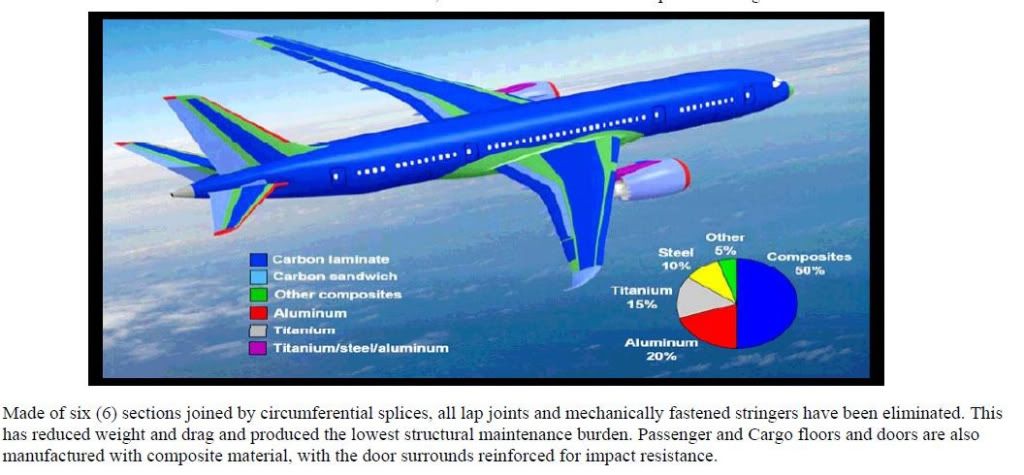
L'inversione di queste proporzioni è un cambio pressochè totale, che ha comportato grandi differenze nelle metodologie produttive nonchè grandi difficoltà. Prima del 787, per esempio, non si sapeva bene come legare materiali cosí esotici insieme, facendoli rimanere insieme anche se sottoposti alle fortissime sollecitazini subite da un aereo in volo: Ricorderete di sicuro, credo, i ritardi generati dai problemi trovati nel raccordo "a cassa" che unisce l'ala alla fusoliera, che continuava a separarsi in strati come una torta millefoglie.
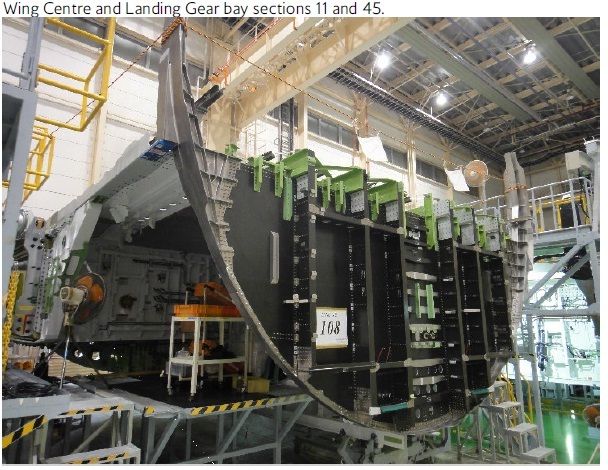
Ed ecco il raccordo "colpevole"
Optare per i materiali compositi ha un effetto sicuramente positivo sui pesi, dato che il carbonio è più leggero, flessibile e resistente delle leghe di alluminio usate solitamente per la fusoliera degli aerei. Ci sono, però, delle controindicazioni, e nemmeno di poco conto. Una di queste è la difficoltà che si incontra nel "legare" insieme materiali così diversi, un problema che ha afflitto Boeing a lungo, al punto che il primo 787 ad uscire dalla catena di montaggio, salutato dal Presidente Obama, aveva dei giunti ("fasteners", non saprei come chiamarli in italiano) inadatti agli usi aeronautici e, pare, acquistati dagli ingegneri Boeing in un negozio della catena Home Depot. Un po' come se la Fiat presentasse la nuova 500 con dei bulloni comprati a Leroy Merlin, per capirci.
Altri problemi riguardano la costruzione dell'aereo in sé, che viene sostanzialmente "tessuto" da un enorme telaio intorno a una cassaforma, poi "cotto" e infine modificato col taglio al laser dei finestrini e di tutte le aperture come portelli e così via. Ogni pezzo viene ispezionato visivamente per assicurarsi che l'amalgama di fibre, resine e colle sia perfetto.
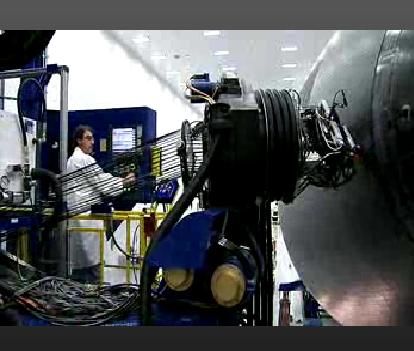
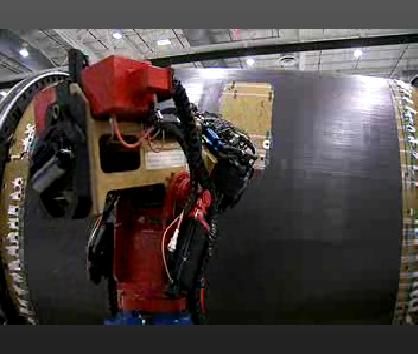
Un aneddoto che mi è stato raccontato e che mi limito a riportare qui, senza poterne confermare la veridicità o meno, dice che la FAA americana abbia costretto Boeing a inserire degli "O ring" metallici, un po' come l'ossatura degli aerei convenzionali, per irrobustire la struttura dell'aereo, rivettandoli alla fusoliera in compositi. Questi anelli non sarebbero stati necessari, secondo Boeing, ma essendo la tecnologia così nuova e rivoluzionaria le autorità hanno preferito non correre rischi.
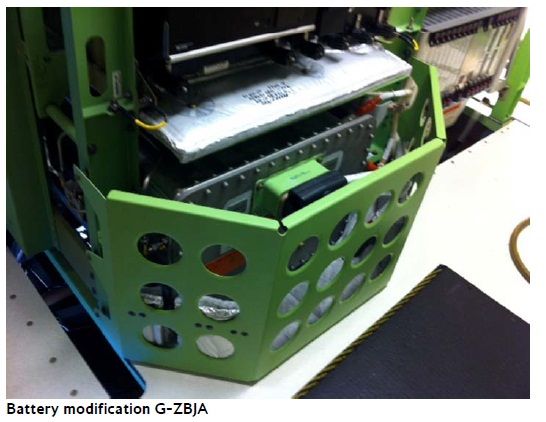
parlando di non correre rischi... Questo è il risultato delle modificazioni per le batterie agli ioni di litio
Un altro problema sono i fulmini. Come forse saprete, gli aerei sono colpiti dai fulmini almeno una volta all'anno, dato che sono l'unica cosa metallica in giro per i cieli. Non è un porlema, i lightning checks sono qualcosa che gli ingegneri sono abituati a compiere e anche l'effetto sui sistemi di bordo è irrisorio, dato che tutto è a doppia o tripla ridondanza. Inoltre gli aerei sono accuratamente schermati, essendo vere e proprie gabbie di Faraday, il che fa sì che la carica elettrica del fulmine possa correre da prua a poppa senza problemi, finendo scaricata dalle prese statiche (quelle piccole antennine che si vedono sulle ali). L'unica parte dell'aereo che non è in metallo è il radome, che non è altro che una specie di guscio di materiale simile alla cellulosa sagomato a nido d'ape; ciononostante, persino quella parte dell'aereo è schermata, grazie a delle lamelle metalliche che corrono verso il muso del radome.
Tutti questi accorgimenti, sul 787, non sono possibili. Il 787 è fatto di grafite e altri materiali non metallici, che non consentono una buona conduzione dell'elettricità. Un possibile fulmine su un aereo del genere avrebbe effetti disastrosi sull'aereo e sui passeggeri a bordo. La soluzione trovata dagli ingegneri Boeing è altamente sofisticata, e prevede di inserire filamenti di rame nel "tessuto" dei compositi, rendendo così l'aereo un buon conduttore pur non essendo metallico.
Un'altra grande differenza che distingue il 787 dal resto del mondo è l'elettricità. Tutti gli aerei generano elettricità, con l'APU e i motori (le turbine fanno girare dei generatori che forniscono l'elettricità di bordo, usata in gran parte per alimentare i sistemi IFE). Il 787 genera piu’ di tre volte l’elettricita’ prodotta dal 777 e la maggioranza e’ in corrente continua (piu’ pericolosa dell’alternata, ovviamente). La necessita’ di dover generare piu’ energia elettrica sta, in parte, nella natura fortemente elettronica dell’aereo, il cui cockpit e’ interamente coperto da pannelli LCD multifunzione e che “dialoga” via WiFi con i servizi di terra, ma anche perche’ il 787 e’ un aereo bleedless; in sostanza, non funziona con questo schema:
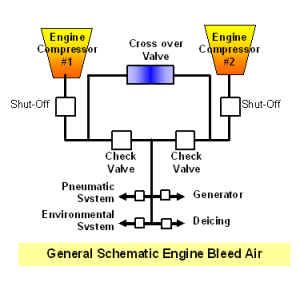
secondo cui i motori di un aereo hanno un particolare compressore che spinge l’aria dalle turbine a un circuito col quale si alimentano generatori, sistemi pneumatici per il controllo di varie parti dell’aereo, il deicing e soprattutto l’aria condizionata di bordo.
Il 787, invece, usa generatori posizionati nei motori (4) e due APU. I generatori collocati nei motori alimentano dei bus in corrente continua che, a loro volta, supportano tutti quei sistemi che prima, erano supportati dai sistemi pneumatici Bleed Air. Per dire, anche i freni sono elettronici!
Il vantaggio di non avere un systema Bleed Air e’ riconducibile alla maggior efficienza in termini di consumi, riduzione dei costi di manutenzione (i sistemi bleed sono notoriamente stronzi da riparare, o almeno cosi’ mi e’ stato detto, dato che bisogna praticamente smontare un motore per accedervi), riduzione dei pesi e, in generale, una maggior facilita’ di utilizzo una volta fatto il “cambio” di mentalita’. Gli svantaggi? Beh, i sistemi elettrici sono meno affidabili di quelli meccanici; bisogna stare attenti alla sicurezza, perche’ stiamo parlando di potenze fino a 540v in corrente continua, roba che uccide, e in generale il costo e’ maggiore. Sappiamo tutti quanto costa farsi riparare un cambio meccanico o uno elettroattuato.
Produzione
In principio il pioniere era Airbus. Il consorzio europeo, infatti, ha creato una delle più complesse (e efficaci) supply chain del mondo, applicando i principi lean all'aviazione civile come mai nessuno prima di quel momento.
Boeing ha sempre prodotto buona parte dei suoi aerei negli USA, se escludiamo componentistica minore e il supporto delle cosiddette "Japanese Heavies" (Mitsubishi su tutte). Il 787 è differente, dato che ha una supply chain che copre almeno tre continenti. Il motivo dietro a questo cambio di politica è duplice: innanzitutto beneficiare dell'esperienza maturata da alcuni costruttori in certi campi e, soprattutto, arraffare quanti più sussidi possibili senza trovarsi l'Unione Europea a protestare al WTO: non è un segreto, infatti, che le Heavies giapponesi sono pesantemente supportate dal governo di Tokyo.
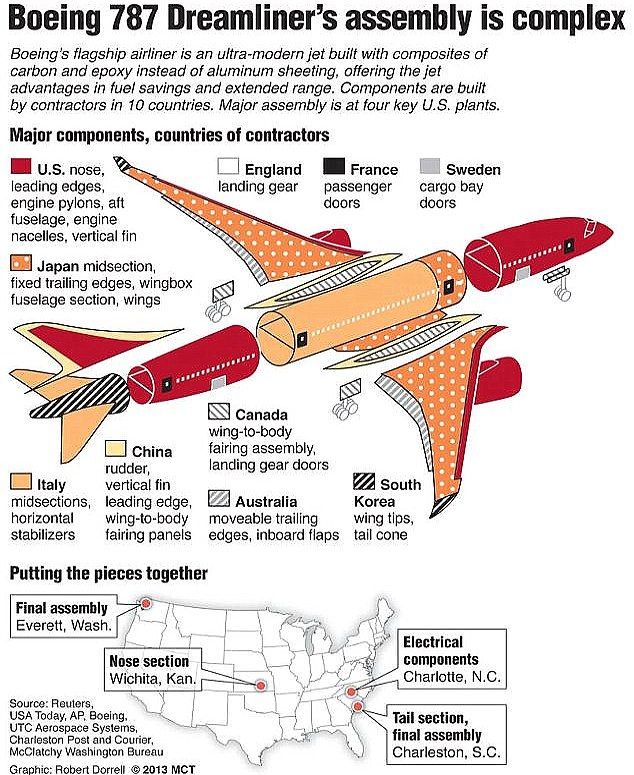
Trucchetti fiscali a parte, la supply chain del 787 è enorme, come mostra questa foto, e la cosa più stupefacente è che funziona. Chiaro, ora la situazione non è delle migliori a causa dei ritardi dovuti alle batterie, ma in generale la catena di montaggio ha dimostrato di saper funzionare, con pezzi in arrivo da posti lontani come l'Italia o il Giappone che appaiono sula linea al giusto momento, nella giusta posizione e nella giusta quantità.
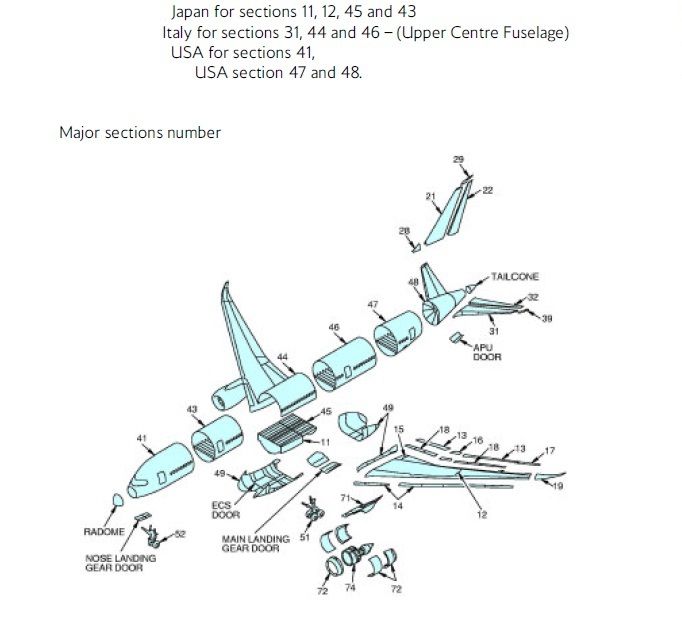
La costruzione dell'aereo in sè è un altro miracolo della produzione lean: ho trovato questo schema, che un collega ha messo insieme dopo essere andato a visitare Seattle, in cui un 787 viene costruito in circa 40 giorni di cycle time. Se pensiamo a cosa sta dietro, alla monumentalità dell'operazione e al fatto che tutto questo non succede per un solo aereo, ma peralmeno una cinquantina di aerei all'anno c'è solamente da rimanere sbalorditi. L'uomo, e so di scrivere qualcosa di veramente nerd, sa macchiarsi delle peggio porcate ma, allo stesso tempo, riesce anche a produrre meraviglie del genere. Anche questa è una "prima" mica da ridere per l'aviazione civile mondiale.
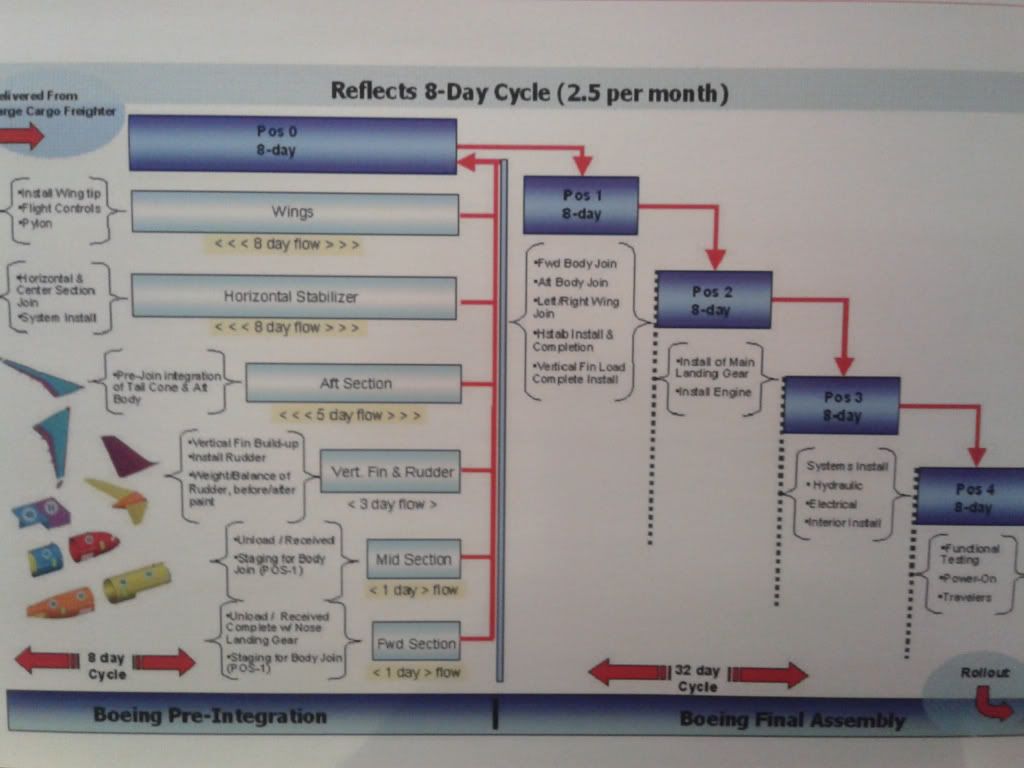
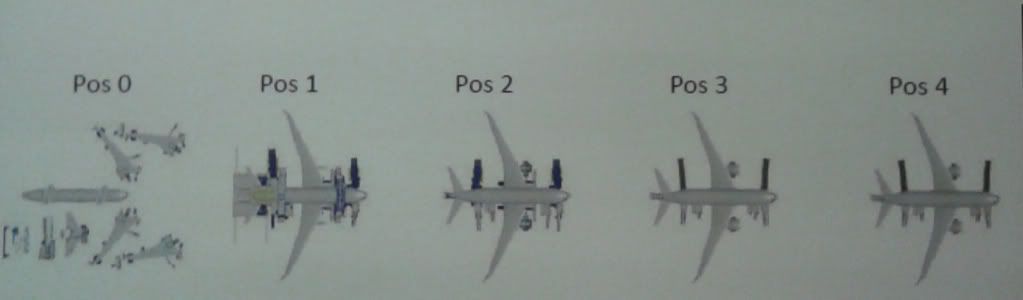
Uso e handling quotidiano
Gli aerei di oggi sono stati costruiti, ideati, negli anni '90, quando i telefonini si portavano nelle valigette, l'unico tablet era stato intravisto in qualche fotogramma di "2001: Odissea nello Spazio" e non esisteva il WiFi. Il 787 è, invece, figlio di quest'epoca, e poco ci manca che non abbia il suo account Twitter per postare i suoi status a amici e followers.
Il risultato è una vera e propria rivoluzione copernicana per chiunque abbia a che fare con l'aereo a terra. Iniziamo con persone come loaders, catering e pulizie, senza dimenticarci dei turnround managers: tutta gente che deve attaccare qualcosa all'aereo: camion, high lifts, elevators, belt conveyors, jetways... Tutta roba di metallo, parecchio pesante, che viene accostata a un aereo. Si tratta di manovre molto delicate, dato che basta perdere un attimo il pedale della frizione per sbattere contro l’aereo e fare danni anche importanti.
Il problema per il 787 e la sua fusoliera in compositi e’ che i danni non sono immediatamente visibili. A differenza di un normale aereo, come questo 747 colpito da delle scalette lasciate non completamente frenate durante una giornata di vento, il buco sulla fusoliera non e’ visibile ad occhio nudo e, peggio ancora, non e’ riparabile con una semplice “pezza” rivettata sulla fusoliera.
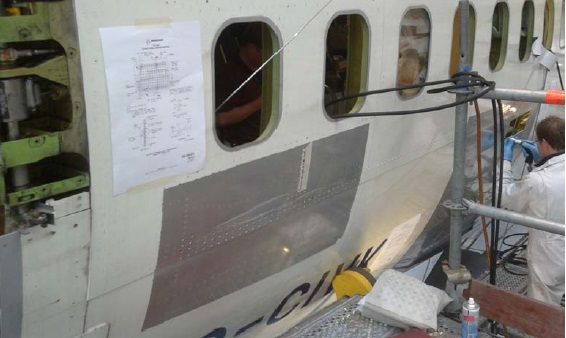
Bisogna, infatti, portare l’aereo in hangar, controllare la trama e l’ordito del “tessuto” con degli strumenti appositi come quelli qui sotto, e agire di conseguenza. Se il danno e’ piccolo si possono introdurre delle schiume specifiche, se il danno e’ grave... meglio non pensarci.
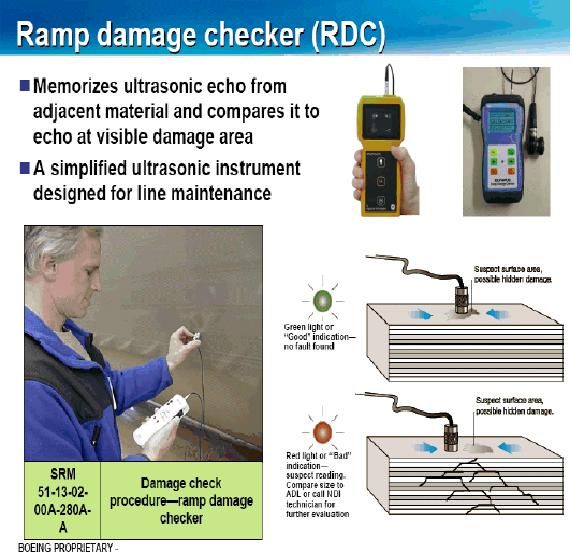
Altri problemi riguardano il layout dell’aereo in se’. Il 787-8 e’ un aereo con 4 uscite, e di solito le jetways attraccano alla porta 2L che, su questo modello, e’ pero’ molto vicina al margine dell’ala, rendendo l’attracco difficile. Anche la 1L non e’ cosi’ facile da avvicinare, dato che la flangia della jetway si troverebbe a meno di quaranta centimetri da una particolare antenna, quella dell’orizzonte artificiale.
Il grosso vantaggio per un ingegnere, pero’, e’ quello di sapere subito come un aereo “sta” al momento dell’arrivo. Il 787 puo’, come dicevo, dialogare via WiFi con i computer degli ingegneri in ufficio sin dall’atterraggio, prima ancora di arrivare on stand. Cosi’ gli ingegneri sanno subito cosa c’e’ che non va e possono intervenire immediatamente, portandosi i pezzi di ricambio direttamente sullo stand.
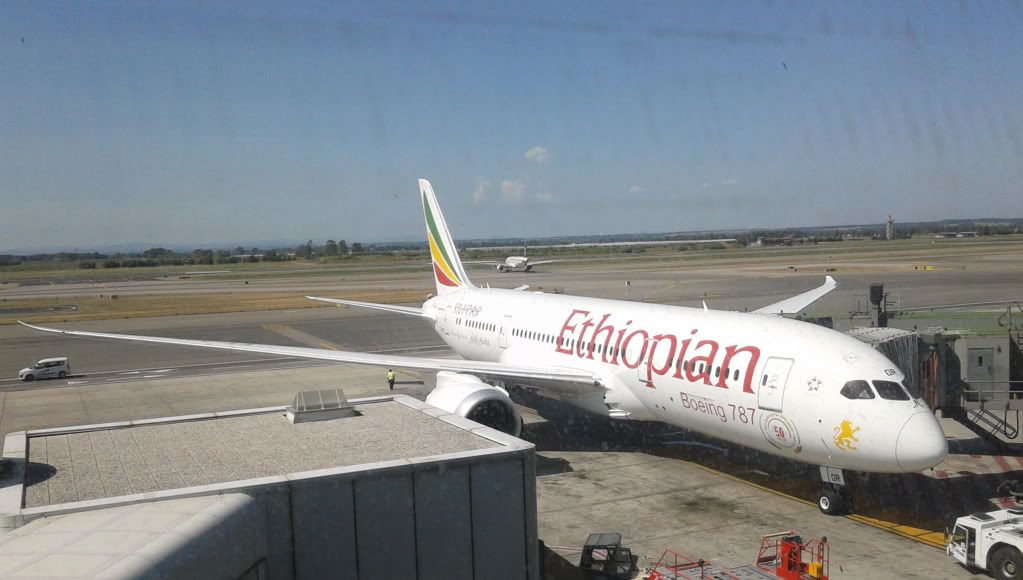
Conclusione
Seven-Late-Seven, l’aereo che riesce a prendere fuoco da solo, la croce della Boeing... Gli appellativi per il 787 si sono sprecati. L’opinione generale sembra quella del personaggio che ho incontrato quel giorno in aeroporto, qualche mese fa: “Com’e’ possibile che, per costruire un aereo che non sembra poi cosi’ diverso dagli altri, ci abbiano messo cosi’ tanto?”
La realta’ e’ che questo aereo e’ diverso in tutto, sottopelle e anche al di sopra. Quando cambiamenti di questa portata vengono apportati, tutti insieme e in un progetto che si spande su quattro continenti, e’ ovvio che ci saranno ritardi, cambiamenti e problemi.
Spero che queste due pagine vi abbiano aiutato a cambiare idea sul Dreamliner, un po’ come hanno aiutato me. E, per finire, una piccola chicca: una preview, limitata devo purtroppo, della Club sui 787 e A380.
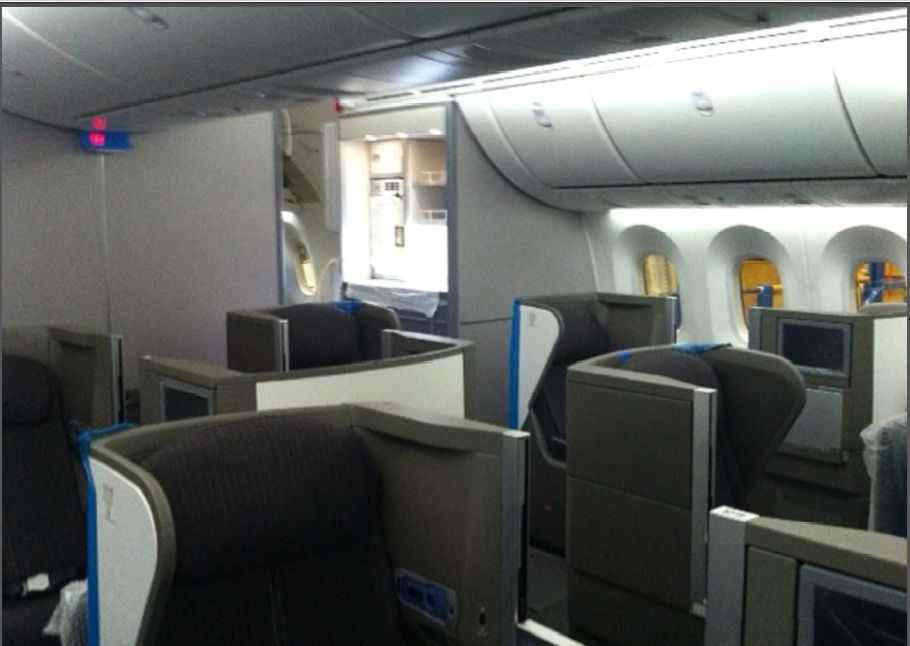
Fonti
- The Boeing Corporation
- British Airways
- Robert Dorrell
- Airliners.net - Russian Spotter Team
Ultima modifica: